To refurb alloy wheels to remove chips, scratches or even just to apply a new look to the paint work, they will require blasting. For those wheels that are already powder coated a acid dip tank is a cost effective way to bring the alloy wheel back to base, efficiently. The alloy wheel would still then need to be blasted to create a profile for the new paint to adhere to and also to remove the imperfections. If the alloy wheel is not yet powder coated then shot blasting from the get go is achievable.
With lots of abrasive grits on the market type of grit can then become a mind field. For use in a shot blastng cabinet you have chilled iron, aluminium oxide, and also steel grit as an options to use. The most popular grit that we come across alloy refurbs using is Aluminium oxide, this is a bit softer then chilled iron and maybe more preferable if already used an acid dip. Alternatively chilled iron and steel grit are a harder abrasives and may be seen to get the job done quicker. For those readers who are more interested in refurbing there own allow wheels rather then doing this as a profession, a cheaper alternative would be to use glass grit fine grade which i have heard to be quite effective, and can be done with a hand held pot. Obviously much more time consuming to get the professional look but should satisfy those DIYers out there.
Now unfortunately that is not the end of this journey to identify blasting grit for alloy refurb, we now have the question of grit size. This can be down to trial and error, and while we have some refurbers using a very fine aluminium oxide at a size fepa 180 we also have plenty using a coarser grades F54 and F70 and even F36. As the grit can be reused up to 20 times it does mean the particle sizes get smaller over time which is why some refurbers start of with a coarse grade and then just adding a handful to the pot every now and again when the results are achieving the profile required, in essence creating your own sizing.
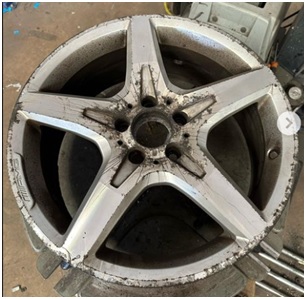
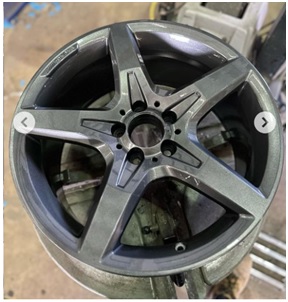
Photos Courtesy of Scuff Medics